THE IBG GROUP comprises over 2500 employees worldwide, 79 consolidated subsidiaries and affiliated companies in 39 countries and has a company history that goes back 100 years.
A company policy that, due to its continuity, ensures a relationship of trust with customers, partners and employees, and makes an important contribution to the achievement of being a leading actor in the business fields of welding and cutting technology, tungsten components and construction chemicals.
IBG is and remains a wholly-owned family business. The backing from our company partners gives us the security to continue on our successful path in the future.
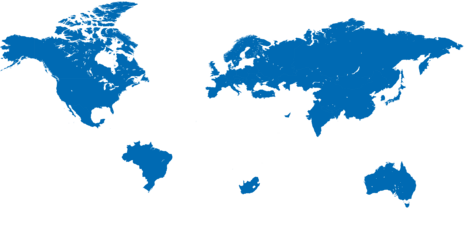
One idea
39 countries. 79 companies
Our worldwide company network with our own production and sales companies, as well as logistic centers, creates the necessary proximity to customers for ensuring complete market coverage. To find out in detail where the IBG Group is internationally active, look at the pages of our individual companies involved in the three business sectors Welding Technology, Tungsten Components and Construction Chemicals.